|
|
Control Strategy Of Battery Management System |
—— Overview
The battery management system (BMS) monitors the status of each single battery in the battery pack, manages the use process of the battery pack, and maintains the consistency of the state of the single battery in the battery pack, so as to ensure the battery safety and improve the battery life. All electric vehicles (including pure electric vehicles and hybrid electric vehicles) are equipped with BMS, and BMS has become one of the key components of modern electric vehicles.
—— Basic Function
• Collection of voltage, current and temperature signals of single battery
• Insulation resistance detection
• Cell consistency equalization
• Estimation of SOC and SOH of battery state of charge
• Over current, over voltage and overheat protection
• Pre charging control of power bus
• Intelligent charging control
• Collection of total voltage and current signal of battery pack
• Battery pack thermal management
—— System Architecture
This scheme uses the master-slave BMS system architecture, one master control module + several acquisition modules. The master control module and the acquisition module communicate through can, as shown in the figure below.The master-slave BMS is flexible in layout, convenient for maintenance, and suitable for all kinds of pure electric vehicles and hybrid electric vehicles.
—— Software Solution
Because of the diversity and complexity of BMS functions, BMS software is very complex. In order to adapt to different models and upgrade the same model, the software needs to be modified repeatedly, which poses a big challenge to software developers. If the traditional manual programming is used, the development workload is huge, and the maintainability of software is poor, which leads to uncontrollable development cycle and development cost.
Automatic code generation can effectively improve the development efficiency and greatly reduce the workload of controller software development. In most applications, with the help of automatic code generation technology, the development cycle can be shortened by at least 50% and the development cost can be reduced by 80%.
The advantages of using Matlab / Simulink / Ecucoder as BMS software development solution mainly include:
• Automatic code generation of basic software and application software at the same time, without manual integration
• Powerful GUI interface can access and configure the whole basic software directly from the model
• The code is reliable, both code readability and execution efficiency are considered
• At the same time, it provides chip level module library and controller level module library to support the controller hardware developed by users
In the BMS software, the basic states of BMS are divided into several states: power on, ready, high voltage off, high voltage precharge, high voltage enable, fault, etc. the transition logic of each state is shown in the following figure:
Basic state transition logic of BMS
—— Key Technology
Battery equalization:
Due to the battery manufacturing process and other reasons, there are differences between different battery cells, such as electrolyte density and electrode equivalent resistance. These differences lead to that even if the charge and discharge current of each cell in series battery group is the same, the capacity of each cell will be different, which will affect the work of the whole battery pack.Worst case, in a battery pack, the residual capacity of a single cell is close to 100%, and the remaining capacity of another monomer is 0. This battery pack can neither charge nor discharge, and is totally useless. Therefore, it is very important to balance the battery capacity, especially when a large number of battery cells are used in series in electric vehicles.
There are many ways of battery equalization, which can be divided into resistance equalization, capacitance equalization, inductance equalization, transformer equalization and DCDC equalization according to different components used, and passive equalization and active equalization according to different energy directions.
Passive equalization efficiency is low, but the system complexity is low and the cost is low, which is suitable for the equalization of small and medium capacity batteries; the active equalization efficiency is high, but the system complexity is high, and the cost is high, which is suitable for the equalization of large capacity batteries.According to the capacity, balance efficiency and cost of the battery pack used by users, this scheme selects passive equalization or active equalization. Passive equalization equalizes the battery with more capacity through resistance consumption, while active equalization transfers the battery with more capacity to the battery with less capacity to achieve equalization. The comparison of the two equalization methods is shown in the following figure:
Comparison project |
Passive equilibrium |
Active equilibrium |
Balanced components |
Resistance |
Capacitance, inductance, transformer, DCDC |
Balanced approach |
Energy consumption |
Energy transfer |
Equilibrium efficiency |
Low |
High |
Complexity |
Low |
High |
Cost |
Low |
High |
RapidECU |
Support |
Support |
Equalizing current |
100mA-500mA |
1A-10A |
Comparison between passive equilibrium and active equilibrium
SOC Estimation:
SOC describes the remaining power of battery, which is one of the most important parameters in the process of battery use. Accurate estimation of SOC can prevent battery overcharge or over discharge, effectively prolong the service life of battery, and can predict the driving range of electric vehicle. Due to the influence of temperature, aging, charge discharge rate, self discharge and other factors, the battery is highly nonlinear in practical application, which makes it difficult to accurately estimate SOC. Some characteristics of lithium battery are shown in the figure
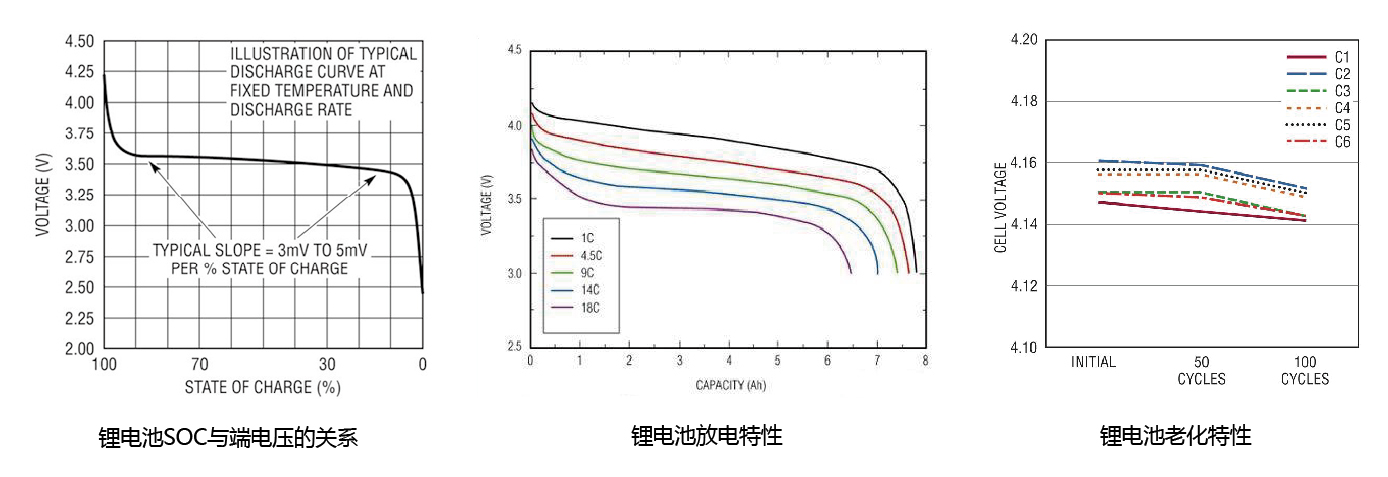
There are many methods to estimate SOC, mainly including:
• Discharge test method
• Current integration method
• Open circuit voltage method
• Load voltage method
• Internal resistance method
• Fuzzy logic method
• Neural network method
• Kalman filter method
There are some defects in the application of the above methods in electric vehicles: the discharge test method needs to interrupt the normal charge and discharge of the battery; the ampere hour metering method has error accumulation; the open circuit voltage method has a large dynamic error; the internal resistance method is greatly affected by temperature; the fuzzy logic method relies on engineering experience; the Kalman filter method relies on the accurate battery model.
SOC estimation method
In this scheme, a SOC estimation method based on ampere hour measurement method and open circuit voltage method under static state is adopted to eliminate cumulative error. The key is to accurately judge the charging and discharging state and static state of the battery. The experimental results show that the SOC estimation error is less than 5%.
Communication protocol:
This scheme uses the communication mode based on CAN bus, which mainly includes three parts:
• CAN communication between main control module and acquisition module in BMS;
• CAN communication between BMS and powertrain control unit such as vehicle controller;
• CAN communication between BMS and off board charger.
|