|
|
BMS hardware-in-the-loop (HIL) test system solution |
Overview
It is not possible to accurately estimate the remaining power of the battery in the current state, resulting in overcharge, overdischarge and other direct damage to the battery; failure to effectively identify various fault conditions such as overvoltage and leakage, which brings serious safety to the battery and the vehicle Consequences; the inconsistency of the single cells cannot be judged. Due to the inhomogeneity of the internal environment, the inconsistency between the single cells increases sharply during the use of the battery pack. There are two reasons for these problems: one is the power battery itself, and the other is the improper use of the battery.
In the power system of electric vehicles, the power battery is always an important part of technology. As an important link connecting battery packs, vehicle systems and motors, BMS controllers must undergo rigorous testing for their functional reliability and safety.
BMS hardware-in-the-loop test simulation system solution
Huahai Technology developed a new energy electronic control test platform based on the SimCar system-BMS HIL, which provides rich and complete test functions for the new energy BMS system. The test system has been widely used in pure electric vehicles, hybrid vehicles and other fields, and has successfully accumulated numerous test cases.
BMS level test
The test principle is shown in the figure above. The BMS main module BMU and the BMS slave module CMU are integrated into the test system. The battery cell simulation board simulates the battery cell voltage and current; the resistance simulation board simulates the cell temperature; the high voltage simulation box simulates high voltage up and down. Power, pre-charge relay control, high-voltage fault simulation functions; at the same time, IO channels are used to simulate switches, sensors and collect the output of the BMS controller.
BMU level test
This test program only tests the BMS main control board, and does not require the slave control board, battery cell simulation board, and battery temperature simulation board. The slave control board is simulated by CAN communication, LIN communication, SENT signal, etc. The rest of the test plan is the same as the BMS level test.
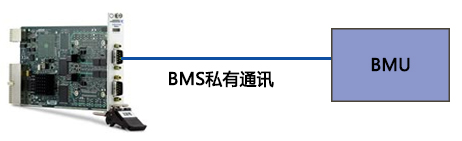
BMS hardware in the loop test simulation system function
Test category |
Test items |
BMS function test |
SOC estimation, SOH estimation, power prediction |
DC internal resistance test, insulation test function test, diagnosis function and management, balance test |
Voltage sampling function, current sampling function, temperature sampling function test |
AC charging test, DC charging, thermal management test, etc. |
Power on and off function, pre-charge relay control, high voltage fault simulation test, etc. |
Battery pack system integration test |
Communication protocols such as CAN, LIN and SENT within BMS |
Synchronous response test of CMC CAN signal |
BMS system (BMC+CMC) network management, sleep wake-up response and other functional tests |
BMS system (BMC+CMC) quiescent current consumption evaluation, low-power state evaluation |
Battery pack system functional safety test |
Single battery short circuit fault injection test |
Temperature sensor short circuit fault injection test |
Temperature sensor open circuit fault injection test |
Short-circuit fault injection test of battery cell sampling line |
Battery cell sampling line open circuit fault injection test |
BMS hardware-in-the-loop test simulation system application field
• Simulation of battery modules or cells
• BMS balancing, insulation and SOC estimation algorithm verification
• BMS power on and off, high voltage fault diagnosis and verification
• BMS charge and discharge, high voltage safety test
• Communication and functional verification based on real vehicle conditions
Engineering experience
Huahai Technology provided a set of BMS hardware-in-the-loop test equipment for a company:
|